Experts in Simulation Engineering
We are a pioneer company in the application of CAE and simulation solutions in a variety of industries since 2003
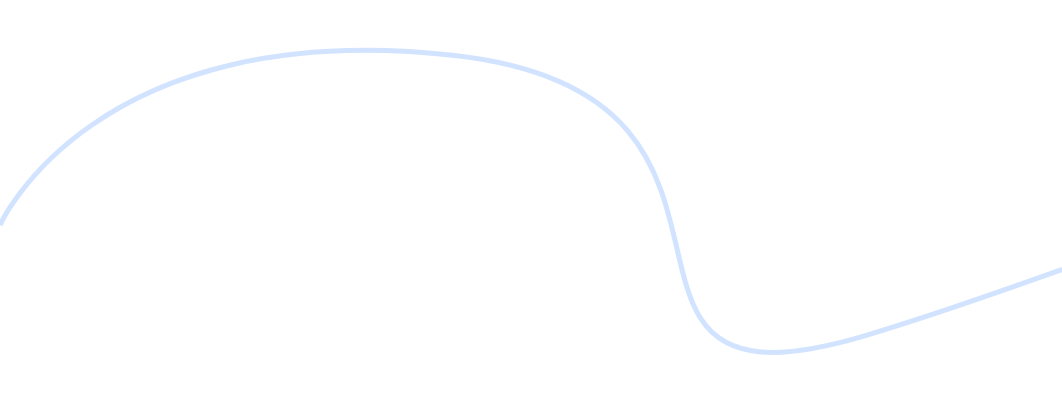
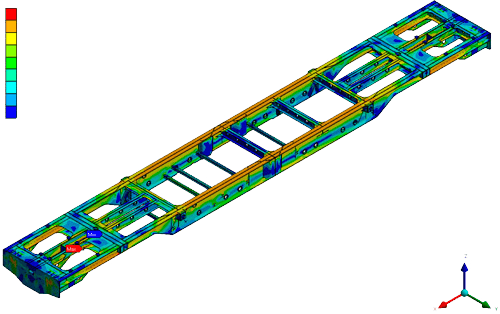
Service
Extensive experience in simulation engineering
Based on an extensive background of more than 15 years, we deliver leading advanced simulation, engineering and consultancy FEA/CFD services around heat transfer and process equipment, non-conventional structures, high temperature piping or ducts systems and a wide range of equipment and structures
FEA - Finite Elements Analysis
The finite element method (FEM) is a numerical technique used to perform finite element analysis (FEA) of any given physical phenomenon.
CFD - Computational Fluid Dynamics
Computational Fluid Dynamics (CFD) is one of the branches of fluid mechanics that uses numerical methods and algorithms to solve and analyze fluid flow problems.
CHT - Conjugated Heat Transfer
The Conjugate Heat Transfer (CHT) analysis type allows for the simulation of heat transfer between solid and fluid domains by exchanging thermal energy at the interfaces between them.
Our value proposal
Cost savings
Manufacturing cost savings (Lean Manufacturing)
Design and optimization
Saving materials and reducing weights
Definition of lightweight materials
Definition of high-strength materials
Definition of high durability materials
Safety & Reliability
Structural integrity analysis
Stability analysis
and / or overturn
Vibration analysis
Modal analysis
(determination of
natural frequencies)
Dynamic analysis
(harmonics,
spectral,
dynamic, PSD)
Simulation of
welding processes
Detection &
anticipation of failures
Evaluation of the useful or remaining life
Fitness For Service FFS Analysis (Aptitude to Service)
Root cause analysis (failure detection and evaluation)
Location and identification of critical points
Fatigue analysis and Creep analysis.
Mechanical analysis of the fracture
Definition of plan of corrective measures
Predictive and corrective maintenance.
Simulation with digital models (Digital Twin)
Time to market
Development of parameterizable designs
Development of modular designs
Lean philosophy
Implementation of agile systems and optimization of design rework
Some of our solutions
-
Railway
-
Naval and defense
-
Automotive
-
Oil & gas
-
Energy Generation
-
Renewable Energy
-
Heavy & special modular structures
-
Lifting equipment, transportation, and cargo handling
-
Piping systems
-
Ducts
-
Urban and industrial furniture
-
Architecture and civil works
-
Design & calculation of joints
-
Non-metallic materials
Naval & Defense
- Submarine hull
- Evaluation of elements of the sealed casing (horn shutter, filters, actuators, etc)
- Structural behavior evaluation of hatches
- Design and calculation of piping and duct systems
- Evaluation of pipe components and online elements (valves,
- Pressure equipment (exchangers, vessels, ...)
- Dynamic and rotating equipment
- Charging elements
- Evaluation of components with some type of defectology (ovalizations, deformations, loss of thickness, cracks, ...)
- Performance of tests
- CFD analysis (internal and external flows)
- Simulation of welding processes
- Root-cause analysis
- Hydraulic and pneumatic system
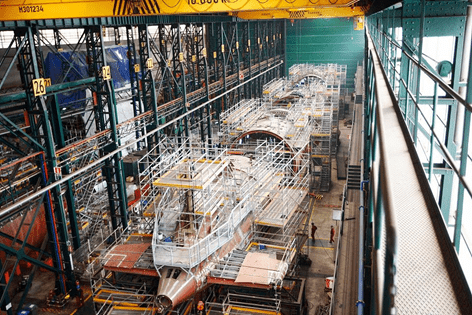
Automotive
- Structural elements
- Engines
- Valves
- Braking systems
- Ventilation systems
- Additive manufacturing
- Topological optimization
- Welding
- Defectology
- Root-cause analysis
- Prototype production
- Impact simulation
- Vibration and noise analysis
- Outdoor aerodynamics
- Refrigeration / climate systems
- Hydraulic systems, pneumatic
- OEM / ODM products
- Industrial vehicles and cargo vehicles (frames, cargo containers, refrigerated containers, etc.)
- Tooling for assembly lines
- Lifting systems
- Paint booths (interior aerodynamics)
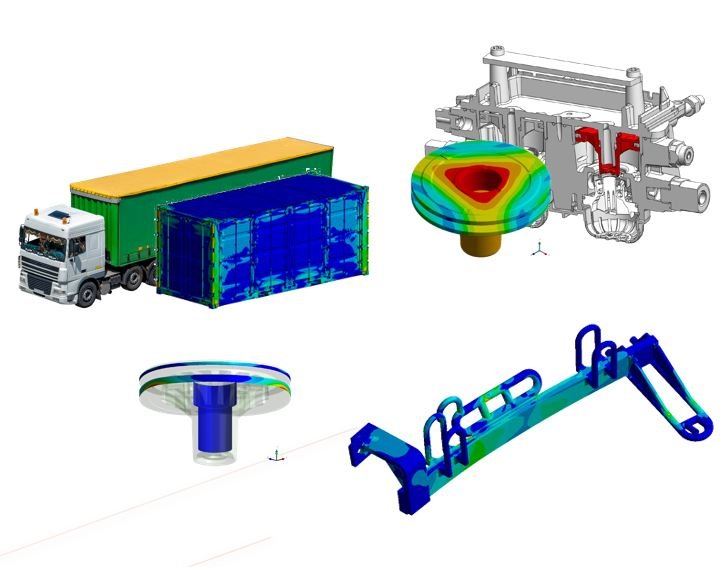
Oil & Gas
- Asset assessment
- fitness for service analysis
- root cause analysis
- boiler equipment:
- chimneys and torches
- pipelines
- pressure vessels
- heat exchangers
- reactors
- columns
- towers
- tanks
- industrial chimneys
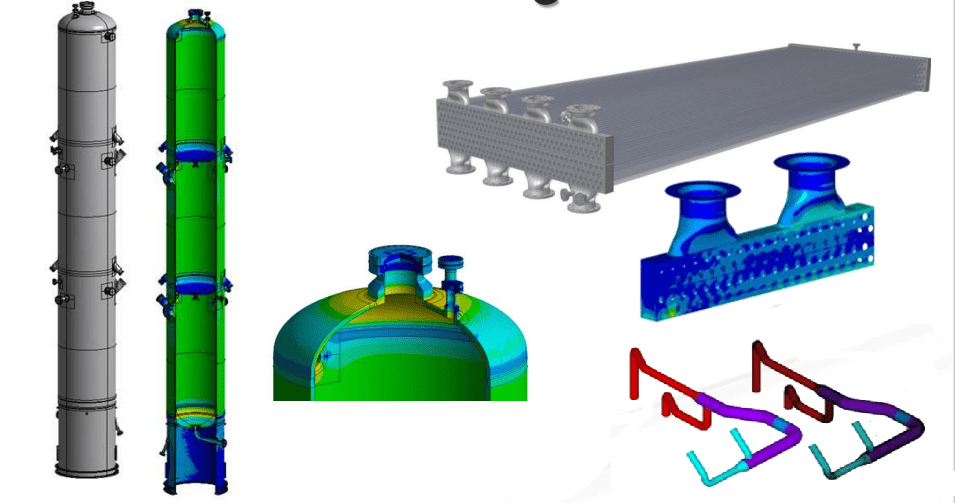
Energy Generation
- Structural integrity
- Fluid dynamic simulation (indoor and outdoor)
- Asset assessment
- Fitness for service analysis
- Root cause analysis
- Chimneys and torches
- Boiler equipment:
- By-pass systems
- Diverters
- Dampers
- Valves (guillotine, butterfly, etc.)
- Gas distributors
- Silencers
- Large diameter ducts
- Pressure equipment
- Exchangers
- Other parts of the equipment
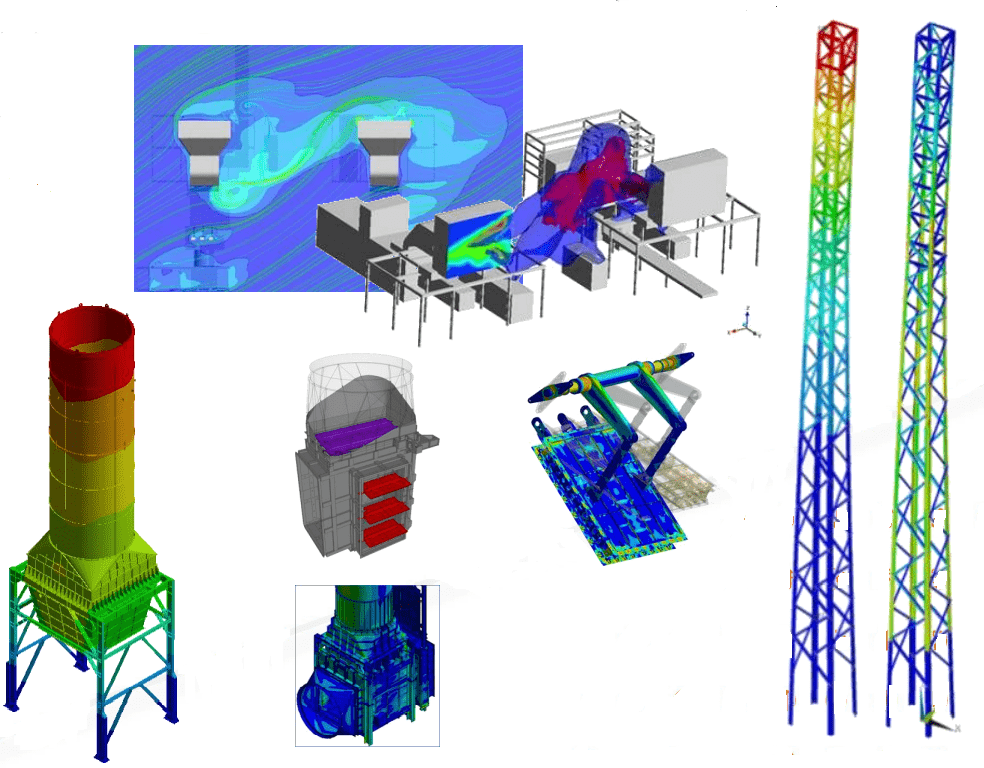
Renewable energy
- Solar trackers (1 or 2 axis solar trackers)
- Concentration structures (parabolic through collector, heliostato, stirling dish, HCPV, etc.)
- Fixed solar structures
- Piping system
- power plants (static equipment and exchangers)
- Dynamic and rotating equipment
- Hydraulic systems (valve)
- Electrification systems
- Wind generators (foundation, towers, bushings, transmission systems, etc.)
- Behavior of screwed joints
- Assessment of useful life or remaining life
- Preventive and corrective maintenance plan
- Root cause analysis
- Definition of the plan of corrective measures
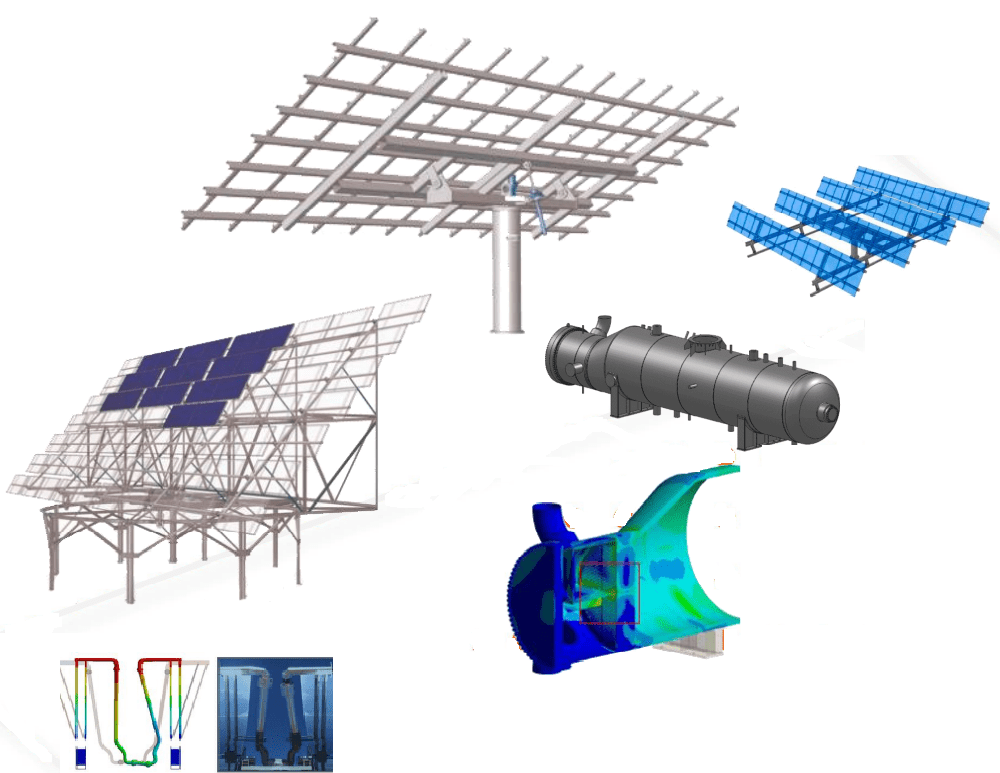
Big structures, special and modular structures
- Steel structures
- Industrial roofs
- Cranes / bridges cranes
- Port cranes
- Channeling infrastructures
- Communication and electrification towers
- Flat or space structural systems composed of bars, plates, walls, sheets, solids and contact elements
- Singular buildings (hangares, etc.)
- Design of modular structures (industrial warehouses, agricultural and livestock warehouses, greenhouses, awnings and canopies, etc.)
- Structures of labeling and corporate image
- Simulation of screwed joints
- Welding process simulation
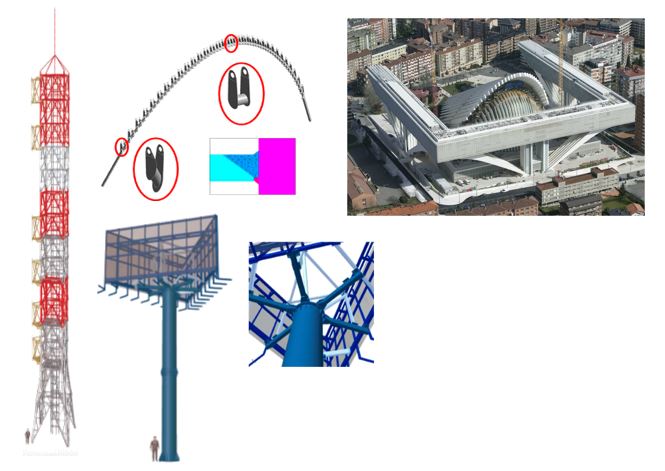
Lifting equipment, transportation, and cargo handling
- Load lifting systems
- Cranes / bridges crane
- Lifting platforms and benches
- Sts, rtg cranes (port cranes)
- Forklifts
- Conveyor belts
- Work platforms
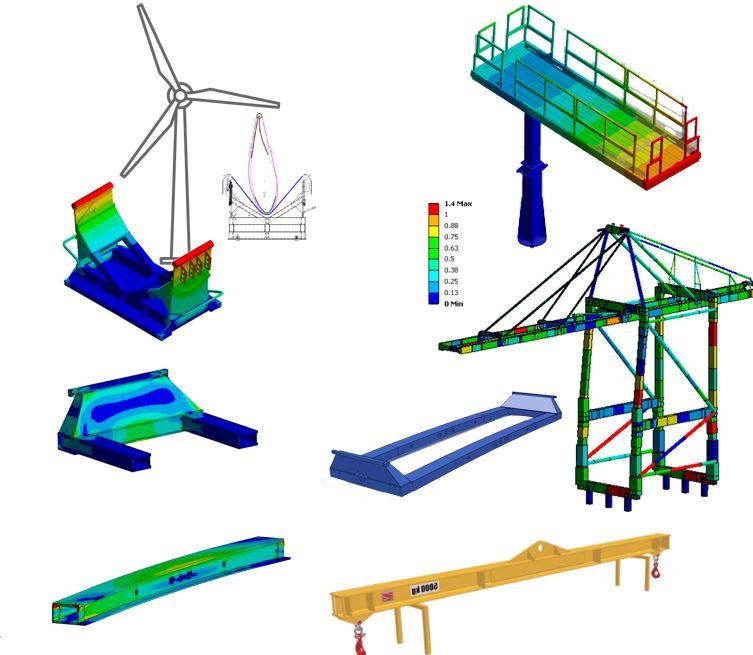
Piping systems
- Stress and flexibility analysis
- Support design
- Special pipes (large diameters, large thicknesses, non-conventional geometries, etc.)
- Online element analysis (TEES, connections, valves, etc.)
- Definition and analysis of expansion joints and compensators (metallic, textiles)
- Analysis of elements under critical loads (high pressures and high temperatures)
- Analysis of thermal trace systems
- Analysis of elements under external pressure or vacuum
- Root cause analysis and fault detection
- Inspection (thickness measurement, 3d scan, corrosion, etc.)
- Definition of measure plan
- Preventive and corrective maintenance
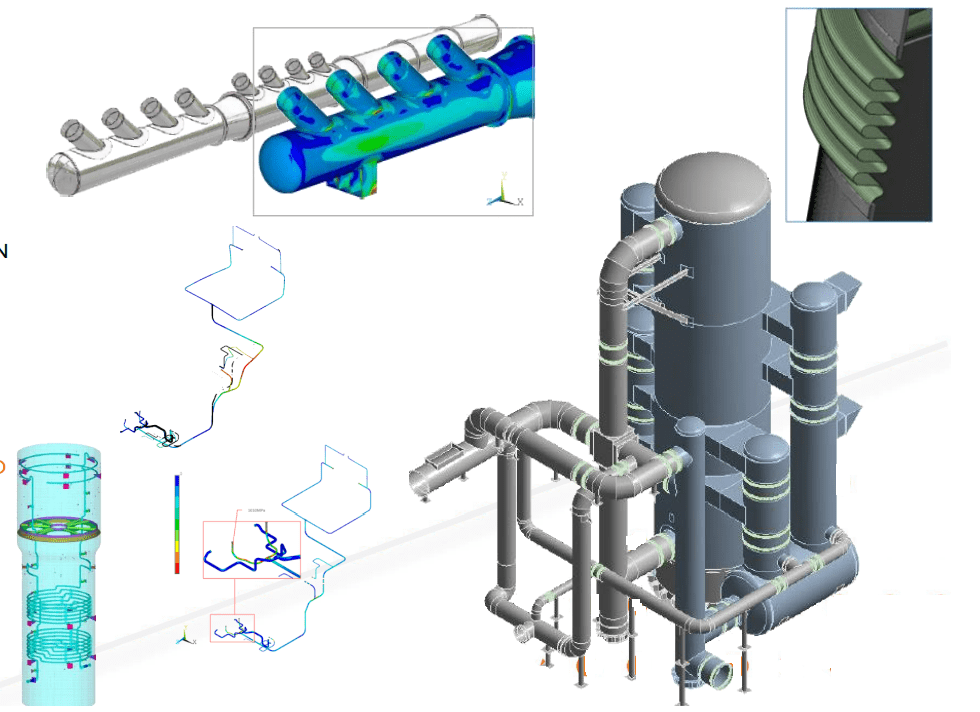
Ducts
- Design and simulation of:
- By-pass systems
- Diverters
- Dampers
- Valves
- Gas distributors
- Silencers
- Large diameter conduits
- Design of support systems
- Online element analysis (tees, connections,
- Valves…etc)
- Definition and analysis of expansion joints and
- Compensators (metallic, textiles)
- Analysis of elements under critical load(high pressures and high temperatures)
- Analysis of elements subject to external pressure or vacuum.
- Fluid dynamic simulation
- Root cause analysis and fault detection
- Inspection (thickness measurement, 3d scan,
- Corrosion, etc.)
- Definition of measure plan
- Preventive and corrective maintenance
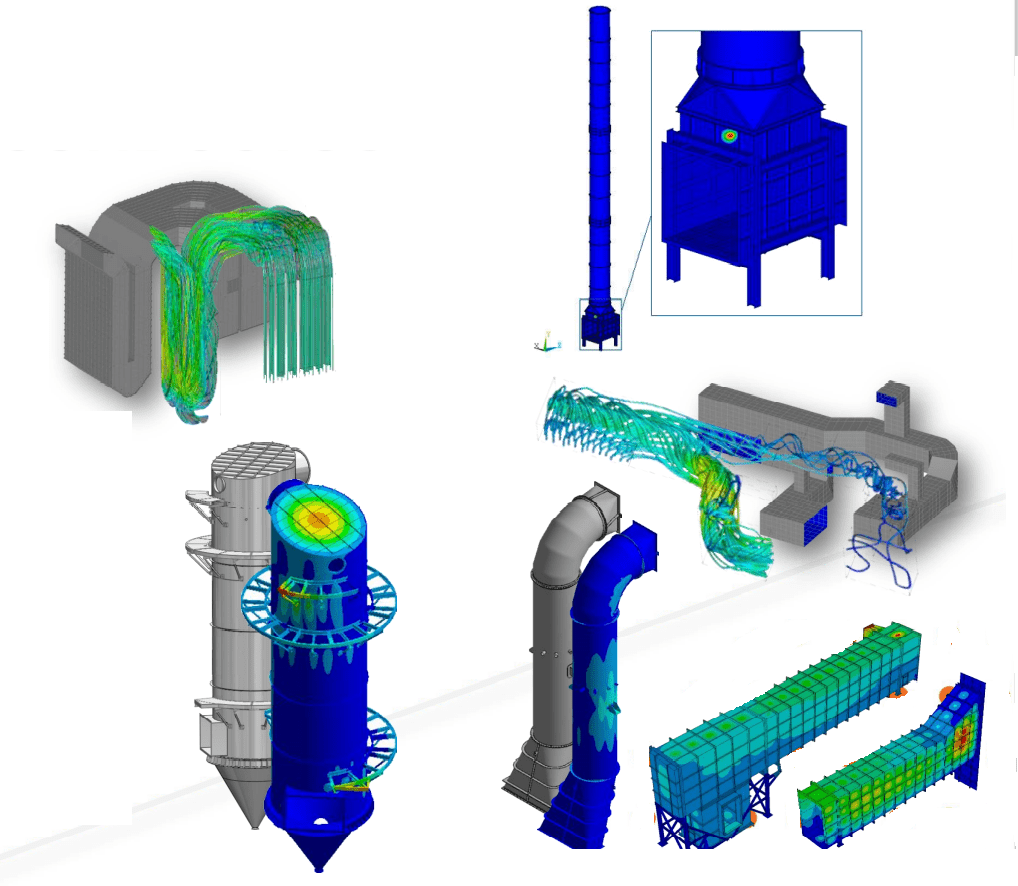
Urban and industrial furniture
- Lighting and lighting system (scales, columns and luminaires)
- Sewer systems, covers, grids ...
- Canopies and pergolas
- Urban furniture
- Recreational furniture (children's parks and sports furniture)
- Industrial storage systems
- Palletization shelves
- Industrial stairs
- Metallic and wood cabinets
- Modular and configurable furniture
- Stands
- Tents
- Structures of labeling and corporate image
- CE marking
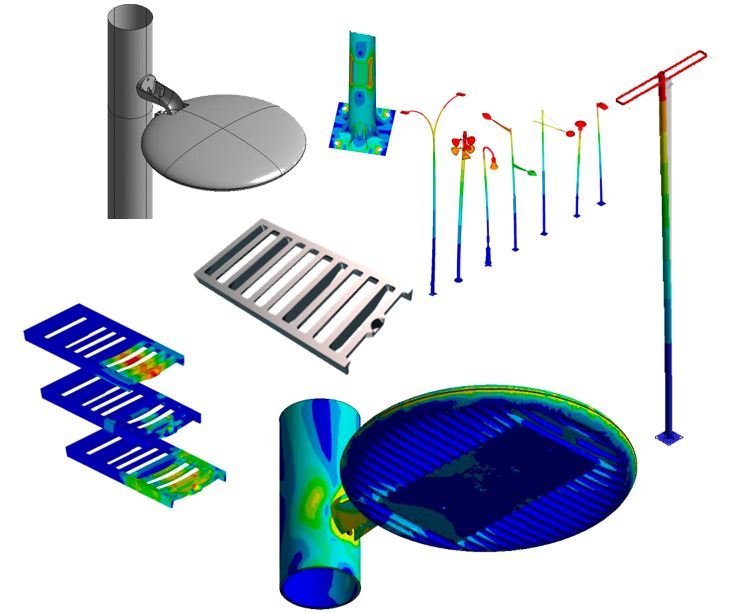
Architecture & civil works
- Buildings / singular buildings
- Covers
- Lifts and staircase
- Electrical equipment containers
- Channeling infrastructures
- Purification of plants
- Adaptation of existing warehouses
- Ventilation and air conditioning systems
- Fire doors
- Explosion doors and windows
- Dynamic analysis and vibrations by resonances
- Seismic analysis
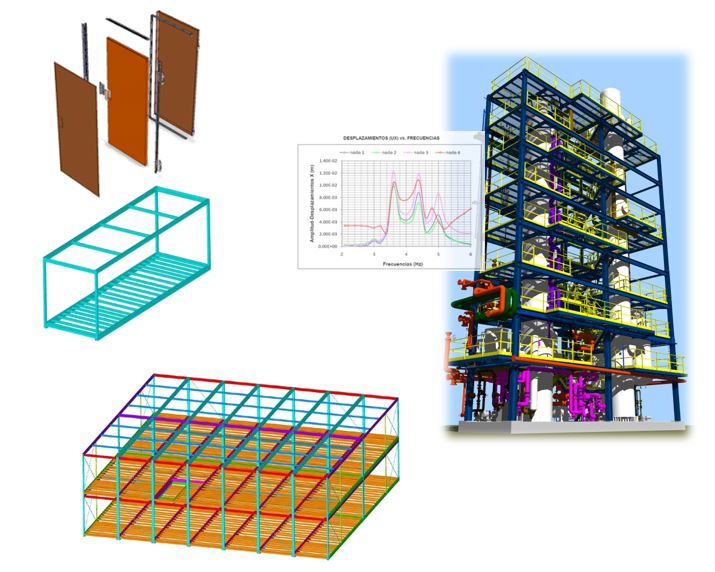
Design & calculation of joints
WELDED JOINTS
- Simulation of welding processes
- Strength calculation of welds
- Construction details design
BOLTED JOINTS
- Design and calculation of conventional screwed joints
- Design and calculation of special screwed joints
- Friction joints
- Definition of tightening torques
- Definition of procedure and tightening sequences
- Conventional screws and high strength screws
- Fatigue calculation
- Palletization shelves
FLANGED JOINTS
- Design and calculation of the joint flanges
- Screw dimensioning
- Definition of tightening torques
- Definition of procedure and tightening sequences
- Assessment of the sealing of the joint
- Base plates and anchoring systems to concrete
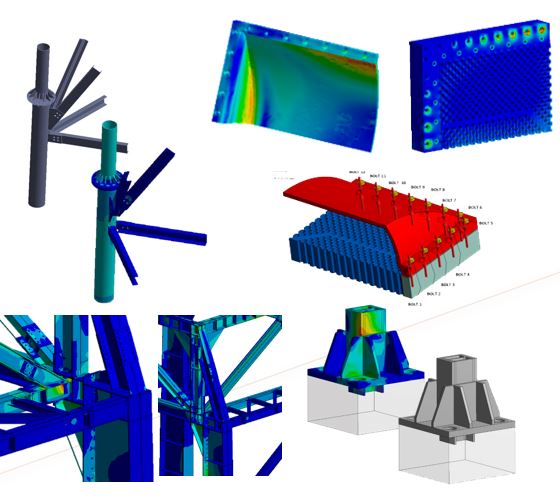
Non-metallic materials
- Pressure vessels cpr
- Design of plastic parts and components
- Design of reinforced polymeric or plastic parts and components
- Plastic injection process simulation
- Material search
- Materials check
- Design of reactors and equipment for plastics production
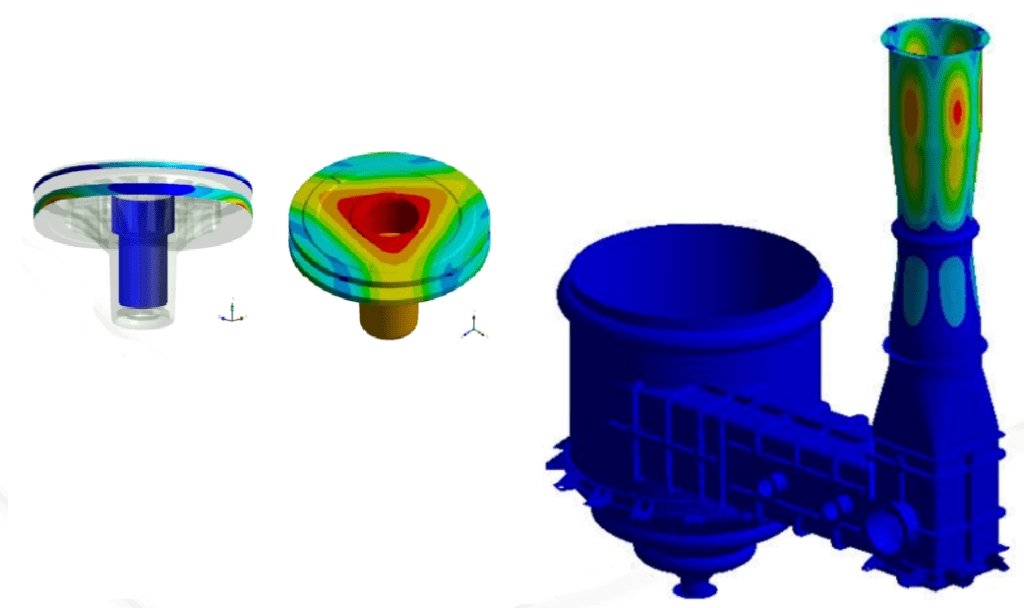
FEM Analysis
Finite Elements analysis
The finite element method (FEM) is a numerical technique used to perform finite element analysis (FEA) of any given physical phenomenon.
It is necessary to use mathematics to comprehensively understand and quantify any physical phenomena, such as structural or fluid behavior, thermal transport, wave propagation, and the growth of biological cells. Most of these processes are described using partial differential equations (PDEs). However, for a computer to solve these PDEs, numerical techniques have been developed over the last few decades and one of the most prominent today is the finite element method.
- Thermal / Structural Transient Analysis
- Dynamic Analysis (modal, harmonic, spectral, PSD, explicit, (…)
- Non-Linear Analysis
- Life Assessment, fatigue, and Creep Analysis
- Fracture mechanics simulation
- CHT – Conjugated Heat Transfer Analysis
- Welding process simulation and PWHT analysis
- Composite, gasket, and other nonmetallic materials
- Topology Optimization
- MBD – Multibody Dynamics
- APDL Programming – Customized Analysis Tools
Successful Projects
Quality Customers
Countries
CFD Analysis
Computational Fluid Dynamics
Computational Fluid Dynamics (CFD) is one of the branches of fluid mechanics that uses numerical methods and algorithms to solve and analyze fluid flow problems.
Computers are used to perform millions of calculations required to simulate the interaction of liquids and gases with complex engineering projected surfaces. Even with simplified equations and high-performance supercomputers, only approximate results can be achieved in many cases.
Continuous research, however, allows the incorporation of software that increases the calculation speed as well as decreases the margin of error, while allowing the analysis of increasingly complex situations such as transonic fluids and turbulent flows. The verification of the data obtained by CFD is usually carried out in wind tunnels or other physical scale models.
- Multi-phase Flows
- FSI – Flow-Structure Interaction
- Heat Transfer and Radiation
- Internal Flows Behavior
- Turbulence Modeling
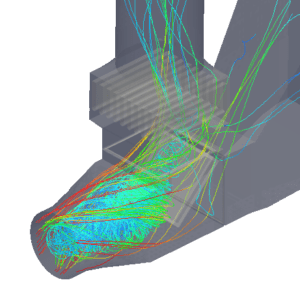
CHT
Conjugated Heat Transfer
The Conjugate Heat Transfer (CHT) analysis type allows for the simulation of heat transfer between solid and fluid domains by exchanging thermal energy at the interfaces between them. Typical applications of this analysis type exist as, but are not limited to, the simulation of heat exchangers, cooling of electronic equipment, and general-purpose cooling and heating systems.
The CHT approach has an advantage over FE thermal analyses in that wall heat transfer coefficients and their local variations on surfaces are directly calculated within the model rather than based on simplified empirical calculations. The CHT approach therefore has benefits for those applications where heat transfer is either non-uniform or difficult to calculate empirically.
Our news
Study of deformations and the prestressing process in pressure equipment flanges
The flanged joints of pressure equipment can show deformations due to the bolt tightening process, or being generated later during service. The appearance of this type of problem may…
Design and FEM analysis of equipment and conductors made of fiber reinforced plastic (FRP)
There are many sectors (chemical and process industry, naval, aeronautical or food sector) and industrial applications in which it is necessary to design and validate…
Fitness for service procedures for cracks like flaws
During the life cycle of many pressure vessels arise the necessity to maintain them in service after detecting crack-like flaws or delamination. For that, there…