CADE’s commitment with our customers always lead us to look for 3D modeling and analysis time reduction in validation and optimization of process equipment and structures with Finite Element Analysis. One handful tool to work on this purpose is the construction of Parameterized models in ANSYS Mechanical APDL and ANSYS Workbench.
One of the most powerful tools that FEM Software ANSYS Mechanical APDL provides in the possibility of working with text commands in APDL language avoiding the use of the graphical interface. APDL (ANSYS Parametric Design Language) is the primary programming language that allows the user to communicate with ANSYS software providing more control and versatility in every operation.
The parameterizing process starts by identifying the analysis processes that can be parameterized; this is a key process in order to carry out an efficient management out and optimize time and resources.
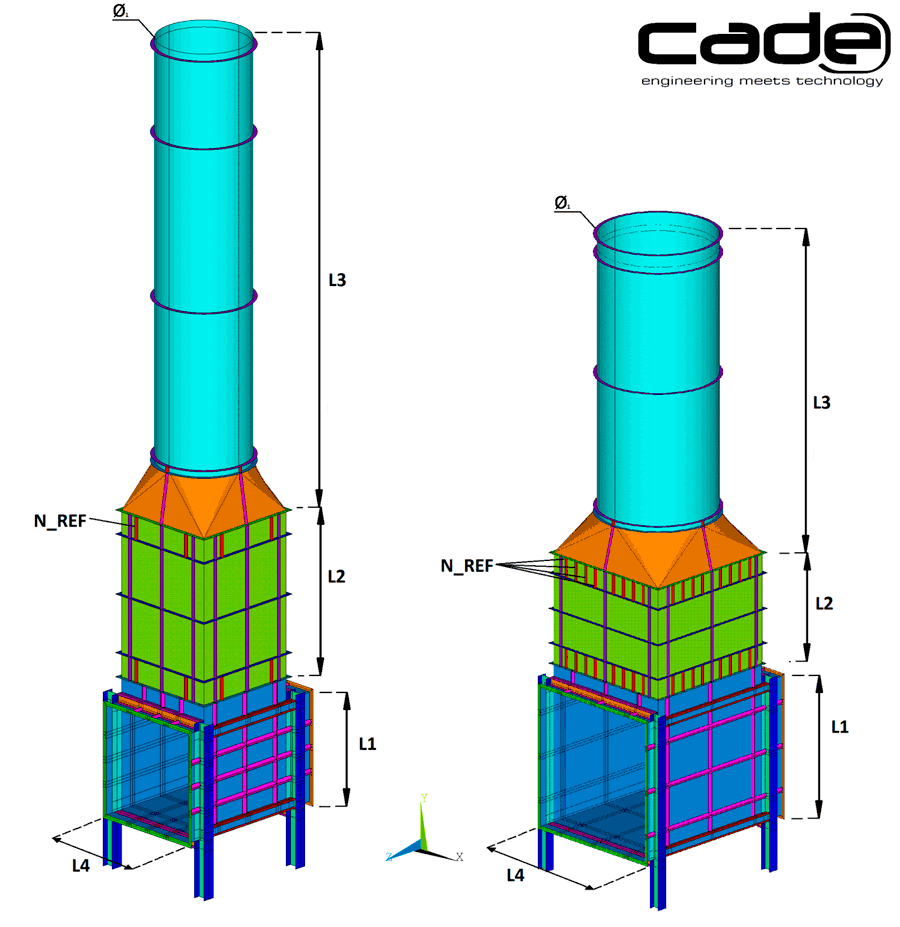
An application example would be the analysis of different structures geometrically similar where might be economically interesting to take some time creating APDL command packages (macros) that can automatically generate the a geometry based in parameters. This time investment will allow the analyst to generate the other similar structures geometries by just a fast change on the parameters values. Likewise parameterization with APDL can be used in other phases of FEM analysis such as meshing, contact definition and postprocessing.
The use of these tools can also be combined with the use of graphical interface so it is possible to standardize only some analyses subroutines that have a high probability of suffer modifications due to design.
Parameterized models are also appropriate for ANSYS Workbench software, which is able to import geometrical parameters directly from CAE models generated in SolidWorks or INVENTOR. Additionally Workbench can also define parameters to create parameterized geometry directly in its Design modeler package. With this method geometry modifications after the analysis is done will not affect the rest of the operations defined after such as contact definition, load application, analysis type or postprocessing options. The correct use of this methodology entails large time reduction in design optimization problems.
The integration of this sort of techniques in CADE’s working methods has lead our expert engineering services to more efficient and accurate solutions and combined with our experience and define cialis know how has help many clients to achieve ambitious and complicate goals.